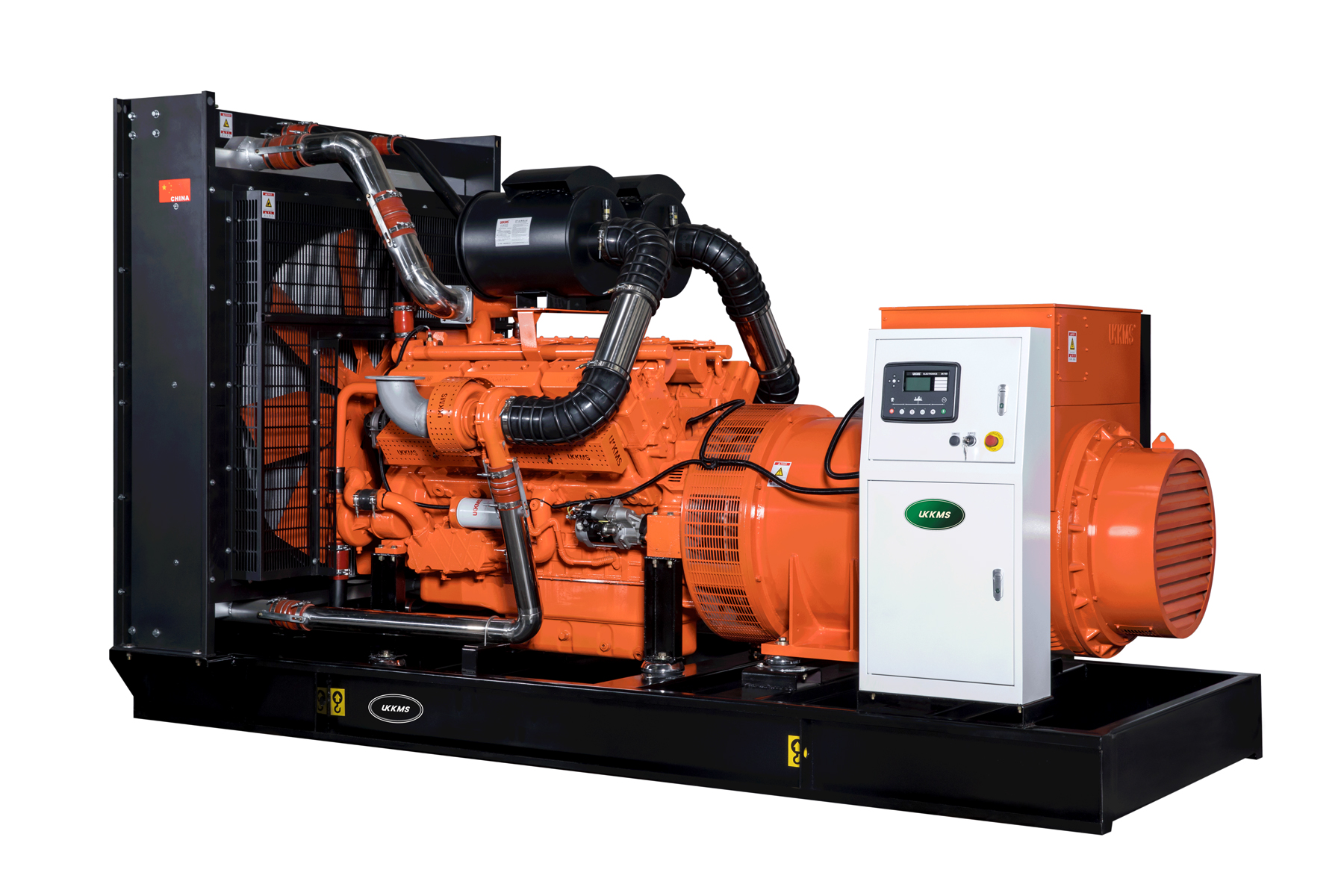
的GWH252-16MW海上风电机组在福建平潭三峡海上风电场成功完成吊装。
按理说,中国碳中和事业搞得如火如荼,一台海上风电机组吊装不是什么新鲜事儿。
但这次不太一样,这台16兆瓦的风电机组是全世界已吊装机组当中单机容量最大的、叶轮直径最长的,还是单位兆瓦重量最轻的,一口气打破了三项全球纪录。
单机容量16兆瓦是个什么概念?就是16000千瓦(kW)的额定发电功率。
这样一台风机只要满负荷工作13.5秒,发出的电量就足够充满1辆特斯拉Model 3的电池包(60度)。
2022年,全中国用电量是86372亿度电,而这一台风机一年发的电量,就足够14亿中国人用满4分钟。
为什么这台大风机特别给力呢?是因为它的扫风面积特别大,5万平米,相当于7个足球场。
这台风机的3支叶片,每一支长度都达到了123米,相当于3架C919客机首尾相连,或者说300个人可以在叶片上同时站立。
它的轮毂中心高度达到152米,相当于3枚长征五号运载火箭摞在一起的高度。
过去我们说,中国在碳中和领域,可能国产化做得最好的是光伏领域,硅料、硅片、电池片、组件,我们已经实现了全产业链自主可控。
而这一次的16MW海上风电机组,在诸多关键领域都做到了非常高水平的国产化。
而现在,金风科技不仅蝉联数年全球风电整机厂商前三名的宝座,他们还联合众多上游配套企业,开发出海外整机厂商都没有做出来过的16兆瓦风电整机关键部件。
它充分展现了中国风电产业在技术创新、供应链协同、工程能力、实验测试等方面的综合实力,为全球海上风电发展树立了全新的标杆。
从制造业的角度来说,大风机会给制造环节带来一系列新的挑战,而所有这些挑战都是新的经济增长点,比如这一次成功研制出来的国产化大轴承,国产化的轴承钢,国产化的超长风机叶片,国产化叶片要用到的国产碳纤维、国产化的超大型铸件……这些新的需求会给众多的风电上游企业打开新的蓝海市场,创造出许许多多全新的“绿色经济”就业岗位。
从老百姓用电的角度来说,我们都希望在走向碳中和的时代里,电费不要哗哗涨,最好能不变,甚至用电还能再便宜一些。
这就倒逼绿色能源装备(比如风电机组、光伏组件、储能电池)每千瓦装机的价格,能够通过技术升级和生产过程优化,实现持续下降。只有单位发电能力的能源装备便宜了,新能源发电场站的固定投资强度才能降低,折合成每年每一度电的发电成本才会下降。而风机大型化是风电实现降本增效的必经之路(这个我们会在文章结尾详细分析)。
从风电市场的角度来说,做出具有国际竞争力水平的国产大风机,能增强中国风电产品对全球风电场业主的吸引力,更好地推动中国风电产业链走出去,占领广阔的全球风电市场,与曾经的国际风电巨头一较高下。
问题在于,全球有那么多家风电龙头企业,为什么是来自中国的企业率先做出了16兆瓦的全球最大海上风电机组?
我们要从供应链的角度入手来深入理解这个问题。在这其中,主轴轴承、叶片碳纤维和大型铸件的国产化是最为关键的支撑要素。
2020年底的时候,我们写过一篇风电的深度文章,里面就讲到过,当时国内3兆瓦以上的“大”风机,主轴轴承主要都依赖进口。
而这一次为了16兆瓦的海上风机,金风科技联合洛轴共同研发,推出了国产的16兆瓦风电主轴轴承的国产化。
在金风的大力支持下,不过两年多的光景,洛轴一下子实现了从6兆瓦到16兆瓦的飞跃。
这个过程中,轴承的直径从两米多一下跃升至3.2米,洛轴原有的很多生产设备、生产工艺都派不上用场。
科研攻关小组专门定制了一套新设备,还参考了大量国内外资料,结合以往的生产经验,创造性地开发出一套全新的工艺。
但是16兆瓦的大风机发电时,在主轴轴承的面前,是3根总重量达到一百多吨的巨型叶片在旋转,尤其是风吹过来的时候,会有明显的弯矩作用,轴承必须保证“风车”能长时间、平稳、流畅旋转,这就对零部件加工精度和弯矩状态下的实验室模拟情况都提出了非常高的要求。
比如轴承内部的滚子,它决定了轴承转动时的平稳程度,它的侧面和上下底部有着细致入微的变化曲线,一个看起来纯平的面,其实是一个球基面,最高点跟最低点的落差只有一根头发丝那么宽。
但即便攻克了这些精密制造过程中的难关,洛轴的实验室中也并不具备模拟16兆瓦风机这么大载荷的实验条件——因为全世界之前都没有面临过这样的问题。
于是金风科技就给洛轴分享了很多动态、静态弯矩条件下的国内外技术资料。而金风由于常年在风电整机领域的深厚技术积累,是有能力做出这样的模拟实验的。
所以上下游企业互通有无、信息共享,又解决了主轴轴承研制过程中对设计方案进行模拟验证的关键问题。
16兆瓦风机主轴轴承的诞生,对我国风电行业减少对国外技术和部件依赖性,甚至实现“换道超车”具有标志性意义。
除了主轴轴承,这次123米的超长叶片和叶片当中的碳纤维材料也是16MW风机需要攻克的一大难题。
123米的叶片,一片50多吨,3片要100多吨,用上碳纤维,重量能显著减轻,这对于叶片的运输、吊装、运维过程都有很多的好处。
而且碳纤维形变小,如果100多米长的叶片不用碳纤维做主梁,那在迎面强风中变形的长叶片都有可能把风机的塔筒(“风车杆”)给打坏,所以大风机一定要用上它。
过去长期以来,碳纤维国产化率一直不高。2020年,我在关注到风电的时候,中国风电叶片碳纤维的国产化才刚刚起步。
在风电、氢能、航空航天等下游领域对碳纤维材料旺盛需求的推动下,中国已经成为美国、日本之后,全球碳纤维领域的第三极。
2022年国产碳纤维用量历史上首次超越了进口碳纤维用量,满足了中国市场总需求量的60.5%,这在几年前还是不可想象的。
我们知道,在风迎面吹叶片的过程中,叶片会发生弯曲形变,但是具体到每一个点的受力都是不同的,而碳纤维拉挤板基本是从叶片的叶根一块块铺到叶尖,有些地方受力更大,对材料的考验也就更大。
因为这一次采用全国产的碳纤维,虽然质量水平相比以往提升了不少,但是“世上没有两片相同的树叶”,每一块合格的碳纤维板做出来以后,它们的质量还是有着细微的差别,如果在那些特别“吃劲儿”的部位用上了水平稍弱一点的碳纤维板,还是有可能出现材料强度和耐久性风险。
于是金风科技就展开了全面攻关,重新做了一轮测试,找到碳纤维材料的“短板点”,让新的设计方案能够“包裹住”每一块碳纤维板质量水平的“离散性”。
换句话说,只要是合格的碳纤维,哪怕用在载荷最大、最吃重的叶片部位,也能保证它不出问题,这样经过优化调整以后的方案就顺利满足了16MW风机叶片的质量要求。
除了主轴轴承和叶片碳纤维材料,这次上下游企业之间最有意思的协同创新案例,发生在铸件领域。
铸件,在我们老百姓看来就是一堆“大铁疙瘩”,似乎没什么技术含量,但实际上并非如此。
因为16MW海上风机要用到的铸件尺寸非常大,比如主轴的轴向长度超过5米,直径接近3.5米,厚度能达到200毫米,上游企业之前根本就没做过这种尺寸的主轴。
这个尺寸的铸件,没法一次浇注成型,需要2~3炉铁水浇筑完成,才能形成这么一个大铸件。
但这就意味着,前后两炉铁水浇筑之间是有时间间隙的,前一炉浇筑完的铁水会冷却一会儿,那么叠加下一炉浇上去,铁水状态是存在很大差异的。所以铸件哪些地方要设计多厚,应该先浇这处还是那处,对铸件的成品率和质量都有着很大的影响。
所以金风找了3家头部的铸件厂商进行攻关,结果四五十吨的一个大铸件第一次生产出来,会发现局部存在一些空气气泡,不是特别理想,每家厂商出现的问题还都不太一样。
他们凭借着同上游企业之间多年来建立起的深厚信任,让三家铸件领域的竞争对手坐在了一起,汇总了所有情况,让三家厂商打破隔阂、敞开心扉地去展示自己的成果和问题。
大家互相取长补短,谁也不甘落后,最后把16兆瓦风机所需的各类铸件都成功地做了出来。
竞争者合作的故事讲得很美好,可是问题就来了:另外两家铸件企业拿不到订单,凭什么愿意“陪跑”呢?
原来,金风在这次完成首台16MW海上风电机组吊装以后,后面还有一系列的大兆瓦海上风机订单,可以给到这些优秀的铸件企业。
所有企业都知道,大兆瓦海上风机一定是未来的发展趋势,所以他们都非常看重这次合作,即便不能用在这第一台16MW风机上,他们也通过这次交流掌握了大兆瓦海上风机铸件的生产工艺和关键技术。
接下来,还有很多风电整机龙头企业,正在与这些铸件企业合作打造13MW、14MW的大型海上风机铸件,而这些铸件企业可以将16MW铸件上的经验、技术成功迁移、复用到同其他企业的合作当中。
上下游互相交织的开放性合作,不仅推动全行业向大兆瓦海上风机升级,还让创新技术在更多的下游实践应用中不断地打磨、完善、分享、扩散,让中国风电整机和配套供应链产品在全球风电市场上具有更强的竞争力和吸引力。
你看到的是一台硕大的风车,你看不到的是背后无数人、无数组织机构,在或竞争、或合作的关系下,共同推动了行业发展。
如果没有下游整机企业用富有前瞻性和战略性的眼光,主动升级产品,满足面向未来的海上风电市场需求,那么上游企业不可能主动出击,去通过合作模式同竞争者一道完成新产品研发。
因为创新永远都面临着不确定性和风险:能不能做出来?没人知道;做出来有没有人要?也不知道。
但是要让风电行业朝着“水平更高、迭代更快、实力更强”的方向发展下去,整个行业的革新必须永不止步。
这时候,下游的风电整机企业就起到了一个“供应链链长”的关键作用:哪怕创新的成本高、投入大,也总要有人推动这件事,而作为全球风电整机第一的金风科技就一直承担着开路人的角色。
在中国,很多战略性新兴产业当中,我们都可以看到这样的优秀企业,比如新能源汽车领域的比亚迪,比如信息与通信基础设施和智能终端领域的华为等等。
有些企业会选择把上下游整条产业链尽收囊中,比如比亚迪,自己做电池、自己做电驱、自己做底盘悬架……
王传福曾经说过这样一句话:“我们要造玻璃、轮胎、钢板之外汽车的所有东西。”
然而在市场经济环境中,做“链长”并不都意味着都要“全盘通吃”,这与每个产业当中分工的专业程度、企业家在不同领域的决策精力分配,和兼并整合上下游企业所需的投资强度等因素都有关系。
事实上,通过联合攻关、技术资源共享、专项资金扶持、互相参股、为研发中的创新产品提前下订单……“链长”企业有多种多样的方式,可以盘活一整条产业链上的资源,调动所有协作供应商的创新积极性。
而这一次全球首台成功吊装的16MW海上风机,就是这种“链长”引领产业链创新机制作用下,最典型也最为生动的体现。
一台取得无数创新突破的海上风机,不仅盘活了风电产业,还创造了成千上万的就业岗位,更为推进中国“碳中和”的绿色事业贡献了自己的一份力量。
在研制16MW机组的过程中,金风科技协同了包括江苏、山东、浙江、广东等地的产业链企业超过100家。
经过初步核算,开发16MW项目能促进国内沿海区域每年新增GDP约25个亿,而通过这个项目的建设,可以为社会提供约7000个就业岗位。
领英发布的《2022全球绿色技能报告》就显示,风力发电技术人员是2020~2021年增长最快的绿色岗位(增速接近90%),是2016~2021年增长第二快的绿色岗位(增速达到24%)。
作为当今全球已吊装的最大功率海上风机,其国产化的本质,就是推动产业链上下游共同实现整体跨越式升级。
举一个例子,中国新材料产业在2010年的产值只有6500亿元,而到了2021年,产值达到7万亿元。
正是由于中国新兴战略性领域(比如海上风电)强劲的下游需求拉动,和下游对产品创新的不懈追求,让众多上游新材料领域(比如碳纤维)的制造企业获得了蓬勃发展的新机遇,创造了大量的新就业岗位。
有人说,如果我们不搞大风机,不搞“链长”机制下的创新研发,做更多台小风机,不是一样可以带来就业吗?不是同样需要尺寸更小但数量更多的铸件、塔筒、叶片吗?
这就回到了我们开头提出的那个问题:为什么风机大型化是风电实现降本增效的必经之路?
比如陆上风电,发展时间更长,安装布设起来更容易,所以比海上风电的成本更低。
但是中国中东部地区陆上风资源条件相对一般,而东部沿海地区,海上风资源好,风大、持续时间长,尤其是深远海。
中国陆上风电一年平均发电小时数是2000多小时,而海上风电轻轻松松就能到三四千小时。
意味着同样是1千瓦的风电机组,陆上风机转一年发2000多度电,而海上风机能发三四千度电。
但是海上环境对风机抗台风、防腐蚀等方面提出了更高要求,另外海上施工作业难度大,还需要海缆、海装船、特殊吊具等一系列安装配套工具,所以相比于陆上风电成本更高,发电成本就更高。
在过去,海上风电在成本上同其他已经比较成熟的新能源形式相比,在成本上没有太大优势。
如果我们可以用上更大装机容量的海上风机,发出更多的电,那么很多固定投资和海上作业的成本都可以被“摊薄”。
以这次的16兆瓦风机为例,如果有央国企要在海上投资做一个总装机容量100万千瓦的大型海上风电项目,那么如果采用8兆瓦的机组,需要125台风机,而16兆瓦的机组就只需要63台,能减少大约一半的机位,节约用海面积35%以上。
这其中一个关键就是,建设海上风电场,是需要租用海域的,业主单位是要向地方政府交租金的。至于你在这片海域上用大风机还是小风机,出租方是不管的。
这就是海上风电降低成本的一宝:无论国内国外,每一个管理风电场的业主,都希望同样的面积,交同样的租金,能发出更多的电来,这样卖电收益会更高,在风电机组整个25年的生命周期中,摊到每一度电里的前期固定成本也更低,这就是大型风机的吸引力所在。
另外,海上风机要立得稳当,就要在海底“打地基”。给一台大风机打地基,比给两台小风机打地基要省钱,立一个大塔筒也比立两个小塔筒更便宜,因为材料、工时都更节省。
这样算下来,一个100万千瓦的大型海上风电项目,用16兆瓦风机替换8兆瓦风机,全场基础成本能降低37%,塔筒成本降低41%,总体降低成本38%以上。
另外,因为16MW大风机捕风效率提高,发电量整体能比两台8MW风机提升6%以上。
所以总体来说,风机每千瓦造价能节省13%以上,度电成本降低12.5%,自有资金内部收益率还能提高10%以上。
这就是海上风电机组大型化能够实现“降本增效”的原因,它也解释了为什么从2012年到2022年,全国平均海上风电单机容量从不到3兆瓦一路增长,直至超过了7兆瓦。
如果你熟悉光伏产业的话,这就像当年中国光伏坚持推广单晶硅,最终战胜了多晶硅的道理是一样的。
单晶硅具有更高的光电转换效率天花板,那么用上单晶硅产品,光伏电站单位面积发出来的电就可以更多,相应的,土地租金、施工成本、支架背板胶膜这些与“面积”相关的成本,都会在更多的发电量中被摊得更薄。
据世界风能协会副主席、中国可再生能源学会风能专业委员会秘书长秦海岩透露,十四五期间,中国还在研制20兆瓦的海上风电机组,届时海上风电的成本还有望进一步降低。
现在,中国海上风电已经告别了国家补贴,走向了“后补贴时代”,实现了平价上网(海上风电上网电价与燃煤发电持平)甚至低价上网(比煤电价格更低)。同其他发电形式同台竞技,不仅靠低碳绿色,更要靠经济实惠。
而恰恰是中国人在风电全产业链追求降本增效的过程中,我们发现,很多过去旧有的技术路线遇到了天花板,就需要产业链携起手来,共同创新,才能突破一层又一层成本瓶颈,为接下来的海上风电的长远发展开辟出降本增效的新路径。
而在这个过程中,整个海上风电行业在下游“链长”企业的引领下,朝着更高比例的国产化、更高水平的国产化、单位(千瓦产品)成本更低的国产化方向稳步发展,不仅助力中国早日实现碳中和,更为社会创造了大量新的就业机会,切实推动了许许多多的行业领域共同进步、繁荣。
那就是中国大而全的制造业体系为中国风电行业提供了强有力的支撑,从上游的铁矿石、石英砂、煤沥青,到中游的生铁、钢板、玻璃纤维、碳纤维,再到下游的铸件、塔筒和叶片,最后到成型的风电整机,让我们可以几乎在本国之内,为了一款大型风机的创新,让上下游企业迅速协同起来,凝聚全产业链合力,成就大国制造的典范。
遥想当年,为了提高中国风电供应链的国产化水平,不希望看到海外风电巨头瓜分中国风电市场的局面,国家发改委还特意发布文件要求风电设备国产化率达到70%以上,不满足设备国产化率要求的风电场不允许建设。
而发展至今,中国人不仅做到了风电装备产量规模世界第一、装机规模世界第一,做出了自己的大型风电整机,还在各个关键环节用上了国产的零部件,培养了一大批精通上下游各领域的大国工匠。
在中国大风机走向深远海的漫漫征途上,中国人已经进入了风电技术的无人区,而征服它、探索它的过程,就是实现碳中和宏伟目标的过程,就是在战略性新兴领域创造新就业的过程,就是让千家万户用上绿色能源、共同应对全球气候变化的过程。
我们对未来最大的慷慨,就是把一切都献给现在。在中国1.8万公里的海岸线之外,矗立着的不只是一台台发电的风机,它们更是14亿中国人为美好未来共同奋斗的信心、决心与雄心。
上一篇:【48812】河北省首个重型燃气机组投产供热 每年可削减运用燃煤180万吨
下一篇:湖北秭归:雪后风机